
From the 2024 4th Quarter Pressure
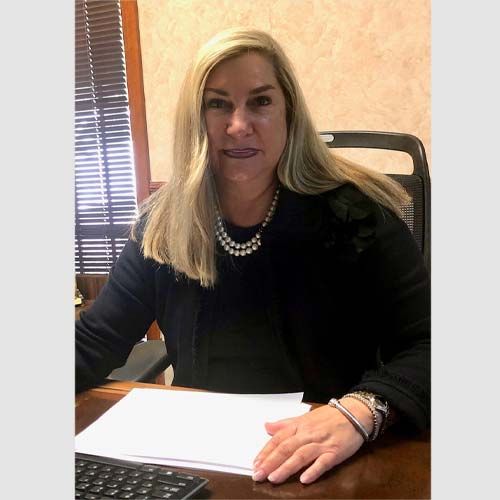
Mary Pat Finn, President & COO Perry Baromedical
Hyperbaric Device Safety: The Fundamentals of Tech Specs & Regulatory Compliance
Regulatory compliance for a medical device manufacturer is a process that continually evolves for the device's lifecycle. In the hyperbaric industry, the ASME: American Society of Mechanical Engineers is the author of the pressure vessel construction standards. In 1911, the American Society of Mechanical Engineers established the Boiler and Pressure Vessel Committee to formulate standards for constructing steam boilers and other pressure vessels such as hyperbaric chambers. The ASME’s function is to establish the rules of safety that govern the construction and design of pressure vessels. (ASME BPVC.VIII.1-2021) These codes and rules provide hyperbaric design engineers’ with the applicable regulations they must follow for the original design of the hyperbaric device throughout the entire device life cycle.
Many people ask me what I am asked the most about hyperbaric chambers; I respond by saying people ask me, “How do I know your chamber is safe.” It is a great question, which I enjoy answering, and I wish more people would ask safety-oriented questions. Safety in the hyperbaric industry is a fundamental aspect of the spectrum of use for providing hyperbaric treatment. Safety is the fundamental theory behind hyperbaric didactic technical training, behind the facility's design, and safety considerations are incorporated into the design codes of the hyperbaric device. Let us take a closer look at the role of the hyperbaric design elements.
To understand the design elements of a hyperbaric chamber, let me share the design inputs that occur during the design process. The engineering team sets out to establish a set of requirements from all the stakeholders. These requirements are design input requirements or (DIR), and they formulate the basis of each complete hyperbaric model design submitted to the FDA for review and approval. The design input requirements encompass certain aspects that could be described as intuitive and some that are driven by regulatory codes and standards. These user requirements could include gurney design and comfort, gurney wheel rolling and locking capability, the height of the gurney, and hyperbaric user technical requirements such as the size of gauges, ability to reach controls, mattress safety and comfort, patient entertainment, ease of use of door handles, door locking mechanism and so forth. In addition, the engineering team will learn the clinical requirements, such as the depth of treatment required, air break needs, gas flow, communications requirements, and other aspects of the design that intersect with the clinical performance of the chamber.
Design inputs then also need to consider the manufacturing environment requirements, which are exhaustive, such as production device considerations to include specialized equipment, staffing, temperature of components, cranes and lifts, lighting, and other aspects that may not be as intuitive in the design process. From there, the input of the quality control team, sales and marketing team, and other related inputs, such as the markets for product sales, must be identified. In addition, practical design elements such as packing and shipping requirements must be understood. Lastly, manufacturing personnel are consulted, and their list of inputs will be considered as part of the design requirements. Obtaining all the design input requirements from external and internal stakeholders is necessary and is part of the formal file submission to the FDA. This process is intended to be exhaustive and considers the needs of every stakeholder, including patients, HBO technicians, physicians, facility, and environmental staff, as well as all those stakeholders at the physical manufacturing plant. The DIR inputs can number into the hundreds to fully ensure the chamber design considers all aspects of medical device utilization.
Now, the most impactful aspects of the DIR are those of the regulatory design input requirements imposed on the engineers. These are critical in terms of the safety and efficacy of the device and are the building blocks for the longevity of the design. These codes and regulations are the fundamental standards that guide the design's structural integrity and the device's ability to perform to the specified requirements. As noted, the ASME formulates the regulations that a manufacturer must follow during the hyperbaric chamber design per these codes and standards. These codes and standards provide the mechanical design inputs to the entire device. These component designs will affect device installation requirements, the installation environment, the operational pressures, the composition of materials utilized, and aspects of the structural integrity of a chamber. The essential codes for designing and manufacturing pressure vessels guide our industry's safety. The codes and standards should include:
Codes and Standards for Hyperbaric Design
- ASME PVHO-1, Safety Standard for Pressure Vessels for Human Occupancy
- ASME Boiler and Pressure Vessel Code, Section VIII, Division 1 – Pressure Vessels
- U. S. FDA Requirement 21 Code of Federal Regulations, Part 820
- NFPA 99, Health Care Facilities
- EN ISO 60601-1, Medical Electrical Equipment Basic Safety
At Perry, The SIGMA series pressure vessels are stamped with the ASME Boiler and Pressure Vessel Code “U” Stamp, stamped with the PVHO-1 Stamp, and are registered with the National Board of Boiler and Pressure Vessel Inspectors. Perry Baromedical Corporation operates a Quality Management System certified to ISO 13485:2016 for the following scope: the Design, Development, Manufacture, and Service of Hyperbaric Chambers. Perry Baromedical Corporation is a Registered Medical Device Establishment. It is important to note that not all manufacturers maintain a “U” stamp or comply with the above standards and codes.
The codes and standards are not only the building blocks for hyperbaric design, but they also become the set of regulatory specifications that a manufacturer must adhere to for the lifecycle of that device. This comprehensive process generates a document called the Technical Service Requirements, referred to as Tech Specs or building services specs, or BSRs. This is the one document above all others that we want to ensure is in front of potential facility operators because it is the official publication from the manufacturer and provides a quick reference to the list of all applicable codes and standards in one easily accessible format. The Tech Spec BSR is where I can point to show a customer which safety standards our devices comply with. The BSRs fundamentally answer and address safety design questions. For hyperbaric facilities in the planning process, this document will help determine the necessary changes and modifications to a hyperbaric suite. It will help shape the critical and essential facility modification needs or build-out requirements. These BSR Tech Specs are the guiding documentation for hyperbaric facility design. With a new hyperbaric location, there are important and impactful decisions for consideration regarding the location of med gas, piping distance considerations and issues, fire suppression needs, lighting needs, flooring type, and essential elements embedded into the hyperbaric BSR technical specifications. An important part of the new hyperbaric facility design is the evaluation of safety measures in this build-out process. The BSRs become the guidance document for review by fire marshals, architects, facility planning teams, and all others involved in the hyperbaric facility design. The BSRs can also be utilized to ensure that a consumer compares applicable devices to applicable devices when completing the due diligence in selecting their hyperbaric equipment. These BSRs are also helpful during a JCAHO or UHMS Accreditation visit. They serve as the ultimate reference document to list the applicable standards for an auditor to review and list the associated FDA 510K number.
While the BSRs are utilized by newcomers to the industry, it can be complex to negotiate the myriad quantity of data found on the internet. Most unfortunately, the adoption of the standards is not uniform across the manufacturers of Class B devices. Specifically, we are encountering devices imported into the US that are not FDA-cleared. This improper importation practice is taking place specifically to get around that device's lack of codes and standards. We are learning that device parts, not fully assembled devices/chambers, are imported into the US and assembled somewhere in the US, posing as a “made in USA product” but only assembled in the US without proper FDA premarket 510K clearance.
So, how does the consumer/purchaser ensure that all the regulatory compliance for said device exists? The best way to ensure device comparison is to obtain the manufacturer’s specifications to delineate: 1. The manufacturer publishes applicable codes; 2. To ensure the device is FDA-cleared, and 3. the device meets the design requirements for PVHO-1. As our industry continues to grow, we all play a role in ensuring proper information is shared and encourage the comparison of chambers. Ask about the manufacturer’s quality management system (QMS). Look up the product listing on the FDA website. Ask about the manufacturer's last quality system audit. All legitimate manufacturers in the US are audited annually. We pay agencies to complete a third-party audit to ensure compliance with our QMS system. Further, when these standards change and are updated, the manufacturer, in turn, must update device standards to continue to comply. Manufacturers participate in regulatory compliance audits to demonstrate to an audit agency that said manufacturer continues to meet companywide QMS compliance to the codes and standards.
Safety and regulatory compliance never stop for the medical device industry. We proudly want our safety record to be reviewed, evaluated, and monitored. We all play a role in the ongoing safety of the hyperbaric industry. Facility operators, physicians, clinicians, architects, engineers, hyperbaric technicians, med gas pipers, and all of us on the hyperbaric device side are working to drive more safety into everything we do. We must embrace and encourage regulatory compliance so that the standards and codes become equally deployed across our spectrum from device manufacture to facility operation.
Submitted By:
Mary Pat Finn, MHA, President
Perry Baromedical Corporation